فهرست عناوین
- اکسیداسیون استالدئید : یک روش صنعتی برای تولید اسید استیک
- تاریخچه اکسیداسیون استالدئید در تولید اسید استیک
- واکنش شیمیایی اکسیداسیون استالدئید
- کاتالیزورها در فرآیند اکسیداسیون استالدئید
- مزایای روش اکسیداسیون استالدئید نسبت به سایر روش ها
- شرایط عملیاتی بهینه برای تولید اسید استیک از استالدئید
- چالش های فرآیند اکسیداسیون استالدئید
- مقایسه اکسیداسیون استالدئید با کربونیلاسیون متانول
- نقش اکسیداسیون استالدئید در تولید مواد شیمیایی دیگر
- تأثیرات اقتصادی استفاده از روش اکسیداسیون استالدئید
نوشته شده توسط شرکت صنایع استیک ایران
منتشر شده توسط شرکت صنایع استیک ایران
تاریخ انتشار مقاله : 17-11-1403
تاریخ بروزرسانی مقاله : 17-11-1403
تعداد کلمات : 1370
آدرس مقاله : لینک مقاله
فرآیند اکسیداسیون استالدئید برای تولید اسید استیک
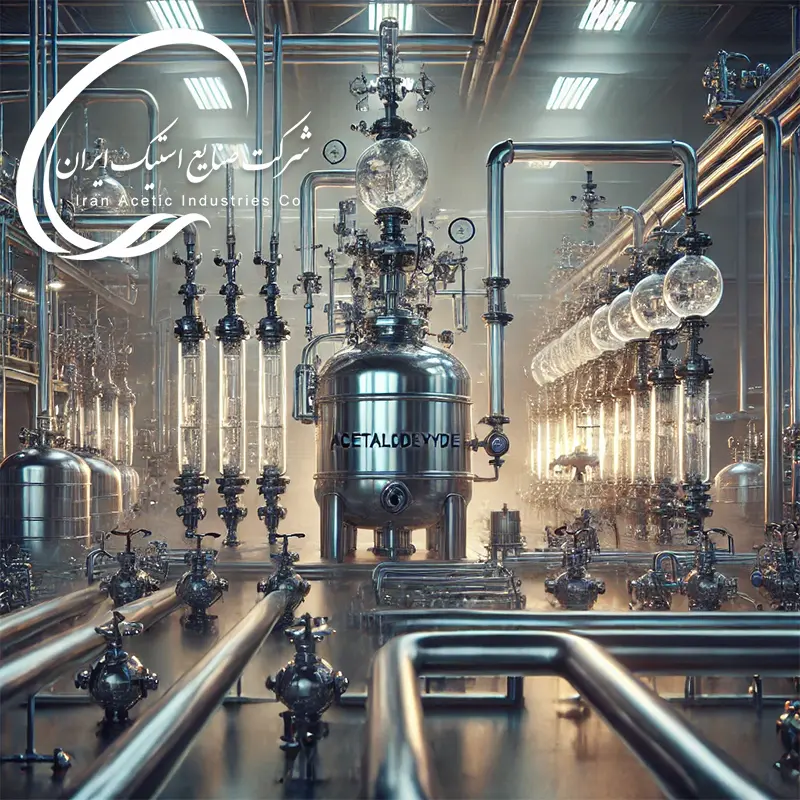
اکسیداسیون استالدئید : یک روش صنعتی برای تولید اسید استیک
اکسیداسیون استالدئید روشی کلاسیک اما هنوز هم کاربردی در تولید اسید استیک است که به دلیل سادگی نسبی تجهیزات و هزینه های عملیاتی پایین تر در مقیاس های تولیدی مشخص رقابتی باقی مانده است. این فرآیند شامل اکسیداسیون کاتالیستی استالدئید (CH₃CHO) با اکسیژن (O₂) است که منجر به تولید اسید استیک (CH₃COOH) می شود. کاتالیزورهای فلزی نظیر نمک های منگنز ، کبالت یا کروم نقش محوری در تسریع واکنش و افزایش انتخاب پذیری به سمت محصول هدف دارند. اگرچه روش های نوین تر مانند کربونیلاسیون متانول از لحاظ بازده و مقیاس تولید صنعتی برتری دارند ، اکسیداسیون استالدئید به دلیل هزینه اولیه پایین تر و پیچیدگی کمتر تجهیزات هنوز هم در برخی از کاربردها و ظرفیت های تولیدی خاص مورد استفاده قرار می گیرد.
تاریخچه اکسیداسیون استالدئید در تولید اسید استیک
تاریخچه تولید صنعتی اسید استیک از طریق اکسیداسیون استالدئید به اواخر قرن نوزدهم باز میگردد. در ابتدا این فرآیند با بازده پایین و با استفاده از کاتالیزورهای نسبتاً ناکار آمد انجام می شد. با گذشت زمان و پیشرفت در علم کاتالیز استفاده از کاتالیزورهای فلزی جدید به ویژه نمک های فلزی مانند منگنز و کبالت به طور چشمگیری بازده فرآیند را افزایش داد. مطالعات گسترده در زمینه مهندسی واکنش ها به کنترل بهتر پارامترهای عملیاتی همچون دما ، فشار و نسبت واکنشگرها منجر شد که در نتیجه بازده بالاتر و تولید محصولات جانبی کمتر را به دنبال داشت. این پیشرفت ها همراه با توسعه تجهیزات کارآمدتر به اقتصادی تر شدن این روش کمک کرد. با این حال ظهور روش کربونیلاسیون متانول که از بازده و مقیاس تولید بالاتری برخوردار است باعث کاهش استفاده از اکسیداسیون استالدئید در مقیاس صنعتی بزرگ شد. با این وجود این روش به عنوان یک فرآیند جایگزین و به خصوص در مقیاس های کوچکتر همچنان مورد استفاده قرار می گیرد.
واکنش شیمیایی اکسیداسیون استالدئید
اکسیداسیون استالدئید به اسید استیک یک واکنش اکسیداسیون کاتالیستی است که در آن یک مولکول اکسیژن (O₂) به استالدئید (CH₃CHO) اضافه می شود. در حضور کاتالیزورهای فلزی مانند نمک های منگنز ، کبالت یا ترکیبات دیگر این واکنش به طور انتخابی منجر به تولید اسید استیک (CH₃COOH) می شود. واکنش به شکل زیر است:
CH₃CHO + ½O₂ → CH₃COOH
مکانیسم دقیق این واکنش پیچیده است و شامل مراحل مختلفی مانند تشکیل رادیکال های آزاد و واکنش های بعدی است. کنترل دقیق پارامترهای عملیاتی همچون دما و فشار برای بهینه سازی بازده و جلوگیری از تشکیل محصولات جانبی ضروری است. دمای واکنش معمولاً در محدوده 50 تا 60 درجه سانتیگراد تنظیم می شود تا از واکنش های جانبی ناخواسته مانند تشکیل استون جلوگیری شود.
مرحله | واکنش شیمیایی | کاتالیست | دمای واکنش (°C) | فشار واکنش (اتمسفر) | محصولات جانبی | زمان واکنش (دقیقه) | کاربرد صنعتی |
---|---|---|---|---|---|---|---|
مرحله ۱ | CH3CHO + 1/2 O2 → CH3COOH | نمکهای منگنز یا کبالت | 50 | 1 | ندارد | 30 | تولید اسید استیک |
مرحله ۲ | CH3CHO → CH3CO + H | رادیکالهای آزاد | 60 | 1 | رادیکالهای هیدروژن | 25 | سنتز کتونها |
مرحله ۳ | CH3CO + O2 → CH3COOO → CH3COOH + O | رادیکالهای آزاد | 70 | 1 | اکسیژن | 20 | فرآوری شیمیایی |
مرحله ۴ | CH3CHO + H2O2 → CH3COOH + H2O | پراکسید هیدروژن | 80 | 2 | آب | 35 | افزودنیهای غذایی |
مرحله ۵ | CH3CHO + MnO2 → CH3COOH + MnO | دیاکسید منگنز | 90 | 2 | منگنز | 40 | کاتالیست صنعتی |
مرحله ۶ | CH3CHO + O3 → CH3COOOH | ازن | 100 | 3 | پراکسید استیل | 15 | مواد ضدعفونیکننده |
مرحله ۷ | CH3CHO + Cl2 + H2O → CH3COOH + 2HCl | کلر | 110 | 3 | هیدروکلریک اسید | 10 | فرآوری پلاستیک |
مرحله ۸ | CH3CHO + NO2 → CH3COOH + NO | دیاکسید نیتروژن | 120 | 4 | نیتریک اسید | 50 | صنایع دارویی |
کاتالیزورها در فرآیند اکسیداسیون استالدئید
این کاتالیزورها سرعت واکنش را افزایش داده و انتخاب پذیری به سمت محصول مورد نظر (اسید استیک) را بهبود می بخشند. انتخاب کاتالیزور مناسب به عوامل متعددی از جمله بازده مورد انتظار و هزینه بستگی دارد. کاتالیزورهای فلزی به ویژه نمک های منگنز ، کبالت و کروم به طور گسترده مورد استفاده قرار می گیرند. این کاتالیزورها به عنوان مراکز فعال عمل کرده و واکنش اکسیداسیون را در سطح خود تسهیل می کنند. ساختار شیمیایی و حالت اکسیداسیون کاتالیزور میزان فعالیت آن را تعیین می کند. علاوه بر فلزات اصلی از پروموترها (افزودنی های کمکی) نیز برای افزایش بازده و پایداری کاتالیزور استفاده می شود.
مزایای روش اکسیداسیون استالدئید نسبت به سایر روش ها
سادگی نسبی تجهیزات مورد نیاز ، هزینه اولیه سرمایه گذاری پایین تر و عدم نیاز به شرایط عملیاتی سخت (فشار و دمای بالا) از جمله مزایای این روش هستند. مواد اولیه مورد استفاده در این فرآیند نیز نسبتاً ارزان و به راحتی قابل تهیه اند. این روش از لحاظ تولید آلاینده های زیست محیطی نیز به طور نسبی کم آلاینده تر از برخی روش های دیگر به ویژه روش های سنتی تر است. با این حال بازده این روش نسبت به روش کربونیلاسیون متانول پایین تر است و این محدودیتی برای تولید در مقیاس صنعتی بزرگ محسوب می شود.
شرایط عملیاتی بهینه برای تولید اسید استیک از استالدئید
به دست آوردن حداکثر بازده در تولید اسید استیک از طریق اکسیداسیون استالدئید به بهینه سازی شرایط عملیاتی بستگی دارد. کنترل دقیق پارامترهای واکنش مانند دما ، فشار و نسبت استالدئید به اکسیژن برای رسیدن به بازده مطلوب اساسی است. دمای واکنش به طور معمول در محدوده 50 تا 120 درجه سانتیگراد نگهداری می شود. در دماهای پایین تر سرعت واکنش کاهش می یابد در حالی که در دماهای بالاتر واکنش های جانبی ناخواسته افزایش می یابند. فشار کار معمولاً در حد فشار اتمسفری یا کمی بالاتر است. غلظت اکسیژن نیز باید به طور دقیق کنترل شود تا از واکنش های ناقص جلوگیری شود. نوع و غلظت کاتالیزور و همچنین طراحی راکتور در بهینه سازی بازده و انتخاب پذیری نقش مهمی دارند.
چالش های فرآیند اکسیداسیون استالدئید
کنترل دقیق دما و فشار برای جلوگیری از واکنش های جانبی و افزایش انتخاب پذیری به اسید استیک ضروری است. نوسانات دمایی منجر به کاهش بازده یا تشکیل محصولات جانبی ناخواسته مانند استون می شود. خوردگی تجهیزات به دلیل ماهیت اسیدی محصول و واکنشگرها یک مشکل اساسی است که نیاز به استفاده از مواد مقاوم به خوردگی در ساخت راکتور و لوله ها دارد. مدیریت و دفع ایمن گازهای جانبی تولید شده در واکنش مانند دی اکسیدکربن و آب نیز حائز اهمیت است. کاهش بازده نسبی این روش نسبت به کربونیلاسیون متانول یک چالش اقتصادی محسوب می شود.
مقایسه اکسیداسیون استالدئید با کربونیلاسیون متانول
اکسیداسیون استالدئید و کربونیلاسیون متانول دو روش اصلی برای تولید اسید استیک هستند که هر یک مزایا و معایب خاص خود را دارند. کربونیلاسیون متانول به دلیل بازده بسیار بالاتر و تولید اسید استیک با خلوص بیشتر به روش غالب در تولید صنعتی تبدیل و موجب کاهش قیمت خرید اسید استیک شده است. این روش با استفاده از کاتالیزورهای فلزی گران قیمت (مانند ترکیبات رودیم) در فشار و دمای بالا انجام می شود. در مقابل اکسیداسیون استالدئید با استفاده از کاتالیزورهای ارزان تر و در شرایط ملایم تر عملیاتی می شود که منجر به هزینه های سرمایه گذاری و عملیاتی پایین تر می شود. سادگی نسبی تجهیزات و فرآیند در اکسیداسیون استالدئید از مزایای آن است. با این حال بازده پایین تر این روش و تولید محصولات جانبی ناخواسته محدودیت هایی را به دنبال دارد. در نتیجه انتخاب بین این دو روش به عوامل متعددی از جمله مقیاس تولید ، هزینه مواد اولیه و قیمت کاتالیزور بستگی دارد. در مقیاس های تولید کوچکتر روش اکسیداسیون استالدئید اقتصادی تر است.
نقش اکسیداسیون استالدئید در تولید مواد شیمیایی دیگر
اکسیداسیون استالدئید فراتر از تولید اسید استیک نقش مهمی در سنتز ترکیبات شیمیایی دیگر ایفا می کند. کنترل دقیق شرایط واکنش امکان تولید محصولات جانبی ارزشمند را فراهم می آورد. به عنوان مثال در شرایط اکسیداسیون ملایم تر پراستیک اسید (CH₃CO₃H) به دست می آید که یک عامل اکسید کننده و ضدعفونی کننده قوی در صنایع مختلف نظیر تصفیه آب و پزشکی کاربرد دارد. واکنش های استری شدن استالدئید با الکل ها منجر به تولید استرها مانند اتیل استات می شود که به عنوان حلال در صنایع رنگ ، پوشش و چسب استفاده می شود. تجاری سازی همزمان اسید استیک و این ترکیبات ارزشمند اقتصاد فرآیند را به نحو چشمگیری بهبود می بخشد و به افزایش منافع اقتصادی می انجامد.
تأثیرات اقتصادی استفاده از روش اکسیداسیون استالدئید
روش اکسیداسیون استالدئید به دلیل سهولت نسبی و هزینه پایین تر در مقایسه با روش های مدرن تر مانند کربونیلاسیون متانول در برخی موارد از نظر اقتصادی جذاب است. در دسترس بودن استالدئید به عنوان ماده اولیه با قیمت مناسب هزینه مواد اولیه را کاهش می دهد. سادگی تجهیزات مورد نیاز هزینه های سرمایهگذاری اولیه را نیز به طور قابل توجهی کاهش می دهد. بهینه سازی فرآیند و استفاده از کاتالیزورهای مناسب به افزایش بازده و کاهش هزینه های عملیاتی کمک می کند. تولید همزمان محصولات جانبی ارزشمند مانند پراستیک اسید، نیز از نظر اقتصادی بسیار مفید می باشد. با این حال بازده پایین تر روش اکسیداسیون استالدئید در مقایسه با کربونیلاسیون متانول محدودیتی برای استفاده گسترده آن در مقیاس های بزرگ تولید است. به همین دلیل مناسب بودن این روش از لحاظ اقتصادی بسته به مقیاس تولید و شرایط بازار متفاوت است.